Industrial Refrigeration Assistance
Your system in 100% operation
Beyond the product. And even beyond customised design. The installation of your solution requires a series of steps for its full functionality, which is best entrusted to a single point of contact. This is especially true in the case of complete turnkey refrigeration systems.
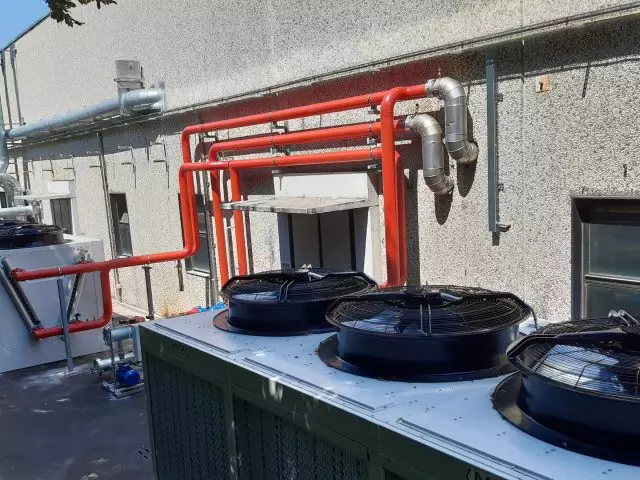
Installation Assistance
The installation phase of the system brings with it practical precautions and prior knowledge of the individual project: why not rely on the same partner who designed and built the machinery and integrated a turnkey industrial refrigeration system?
Go to the pagePlant Connections
Plumbing and electrical connections are of course an important component of the heat dissipation system or turnkey refrigeration system: we entrust this essential phase to serious and trained operators, always with our supervision during installation of the machinery.
Go to the page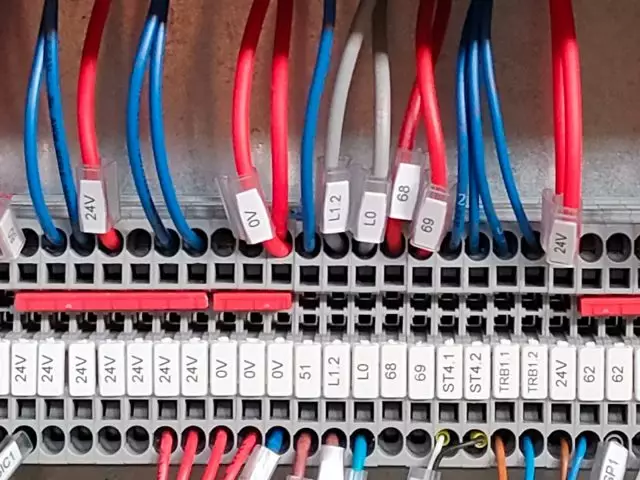
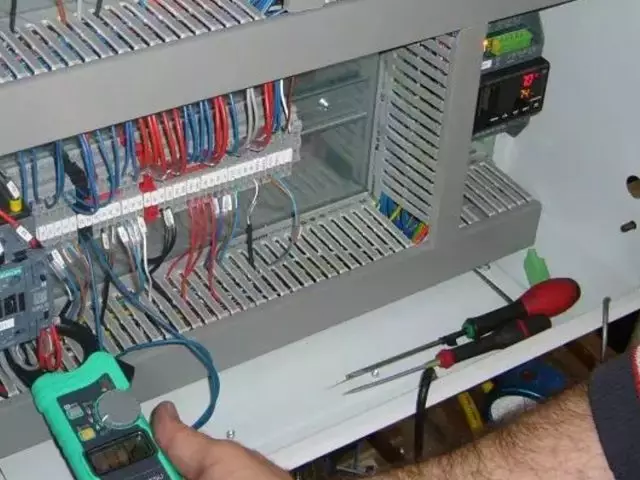
Start-Up Test
The refrigeration or cooling system, or the turnkey system, is installed. The secondary components and piping are also ready. All that is missing is the first start-up: a phase where supervision by your single-source contact person for industrial refrigeration is still important. Here's why.
Go to the pageOperators’ Training
Water and antifreeze filters, control panels and f-gas: every refrigeration or cooling system has mechanical and electronic components to be managed and maintained over time. Need support? No problem. We'll explain everything to you at first start-up. You will also be able to call us for routine maintenance, according to the timetable for an appropriate 'servicing' of the machinery.
Go to the page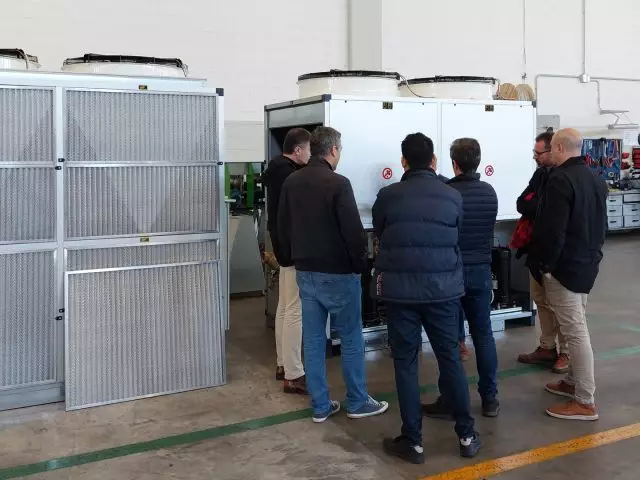
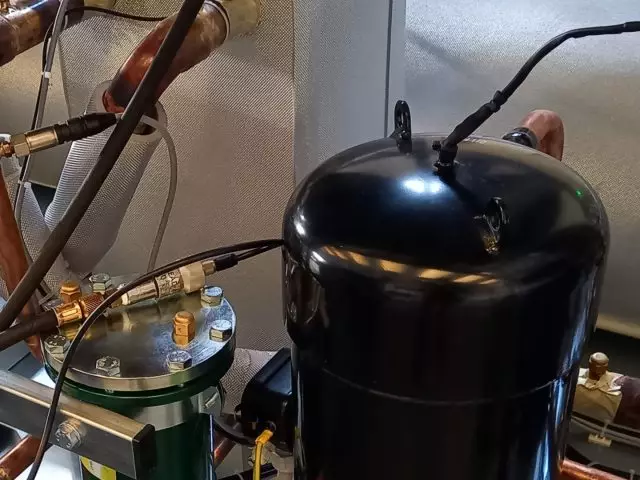
F-Gas Control
If you want to inspect your chiller, and check for leaks, you should contact a certified company: we are at your disposal for inspection and maintenance of chillers, Frigofluid and non-Frigofluid, operating with fluorinated gases.
Go to the pageSpare Parts
Frigofluid supplies you with standard spare parts for all the refrigeration and cooling systems it manufactures. It is important to provide periodic or extraordinary spare parts replacement, in case of critical situations, in order to always have efficient and safe systems.
Go to the page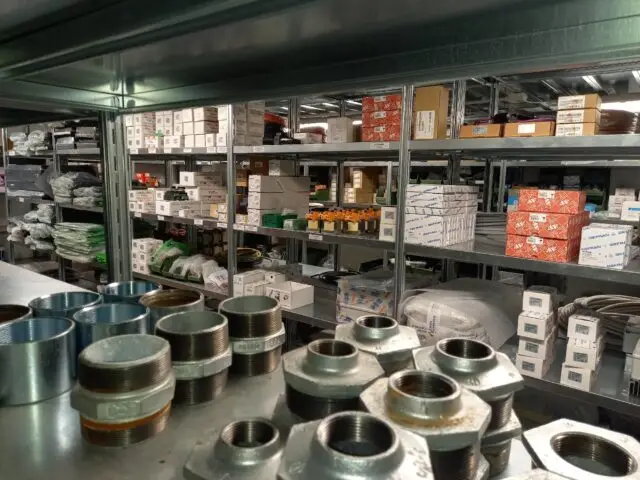
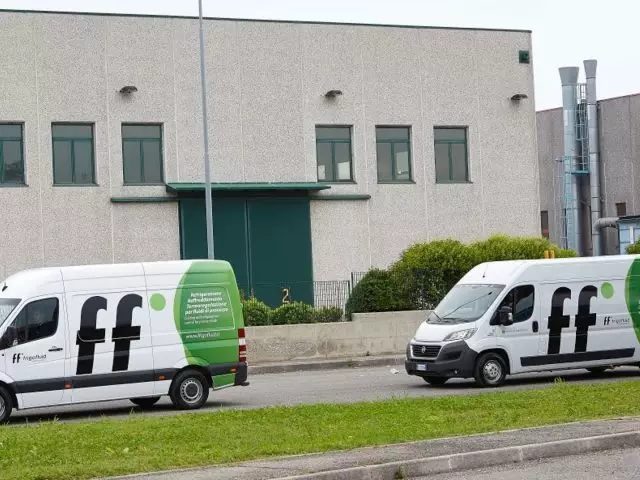
Plant Maintenance
Regular communications, proven practices, mobile workshops and timely intervention by licensed technicians. We won't leave you alone after installation: you can count on us for routine and extraordinary maintenance of your industrial chillers and coolers.
Go to the pageChiller Ready for Delivery
Frigofluid offers a wide range of chillers in stock to meet the needs of customers who are in extremely urgent need of an industrial chiller. Our selection of “ready to pick up” chillers includes several types, including solutions with environmentally friendly refrigerants, others with free-cooling modes, and industrial chillers specifically for low fluid outlet temperatures.
Go to the page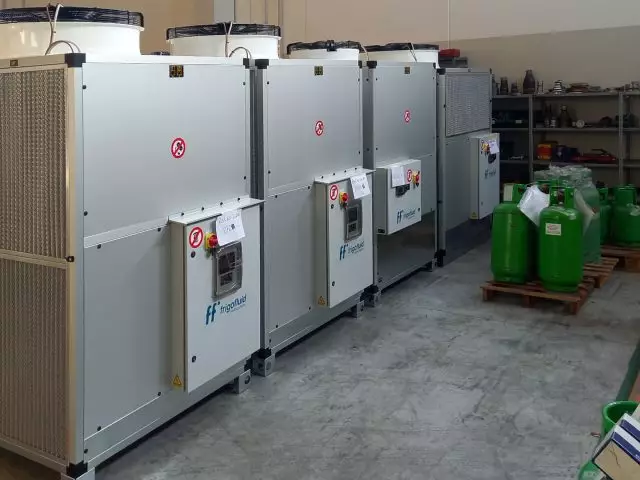
Frigofluid service: precise and effective
Frigofluid is well aware of the importance of after-sales service and, to this end, invests heavily in the training of on-site refrigeration technicians, all of whom have a regular licence, but care and courtesy are also essential with all customers. Fully equipped mobile workshops ensure maximum professionalism and intervention capacity. Training courses for foreign refrigeration technicians are organised to ensure a high degree of customer care anywhere in the world.
Ask for informationResources
Plants and components
Find out all Frigofluid's productsComparing Different Technologies
Find out all the different technologiesFind out more
All technical articlesTools to help you choose
Customized Design
Custom Chillers and Turnkey Plants
Our Newsletter
Subscribe to the Frigofluid newsletter: stay up-to-date on technical solutions for industrial refrigeration and cooling and get to know our offer.